Why industrial rope access might be the smart choice for process industry asset managers
In the demanding world of process industries, where asset integrity, production efficiency, and safety are paramount, choosing the right method for working at height is more than just a logistical concern. It’s a strategic decision that can significantly impact operational downtime and long-term profitability. This is where industrial rope access emerges as a powerful alternative to conventional methods like scaffolding or Mobile Elevating Work Platforms (MEWPs).
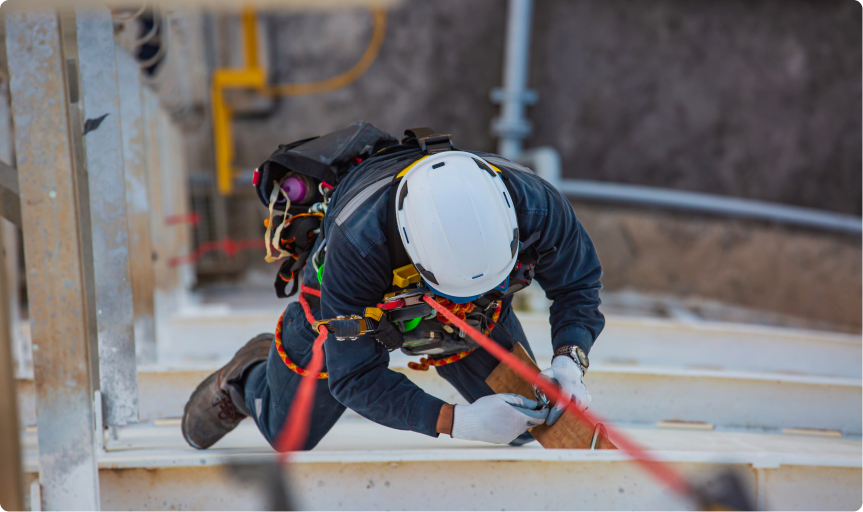
The process industry footprint: Maximising every square metre
Process industries, including sectors like oil and gas, petrochemicals, and pharmaceuticals, are defined by complex infrastructures and tightly packed sites. Every square metre of a facility’s footprint is optimised for production, leaving little room for bulky access solutions like scaffolding or MEWPs. This compact layout makes traditional access methods not only challenging but sometimes impossible.
Rope access, however, requires minimal equipment that can be quickly installed and removed, even in restricted and confined spaces. Workers are suspended from ropes, allowing them to reach virtually any part of the structure without taking up valuable ground space. This flexibility is invaluable in environments where operational areas are already crowded with essential machinery, pipework, and equipment.
Speed and efficiency: Reducing downtime to boost productivity
In process industries, every hour of downtime leads to significant losses issues, not only in revenue loss, but also in production backlogs and project delays. Traditional access methods like scaffolding often take days or even weeks to set up and dismantle, prolonging shutdown periods and hampering overall productivity.
In contrast, industrial rope access offers a faster solution. Setup is quick, often requiring just a fraction of the time needed for scaffolding or powered platforms. Once the work is complete, ropes and equipment can be removed just as swiftly, enabling normal operations to resume with minimal delay. This rapid deployment and teardown are crucial for maintaining the operational efficiency that process industries demand.
Safety first: Why rope access is trusted by professionals
When working at height, safety is a top priority. Industrial rope access is one of the safest methods available, boasting an impressive safety record. According to the Industrial Rope Access Trade Association (IRATA), rope access has a significantly lower incident rate than other forms of work at height.
This exceptional safety is the result of strict operational guidelines, rigorous training, detailed planning, specialist equipment, and continuous supervision. A major advantage of industrial rope access is the built-in rescue planning and capabilities that come with every team. Unlike traditional access methods, which may require dedicated rescue teams, rope access professionals are fully equipped to handle rescue situations as part of their standard operating procedure.
At the heart of this approach is the presence of an IRATA Level 3 technician on every job. These highly skilled professionals are not only specialists in rope access techniques but are also trained in advanced rescue operations, ensuring a quick response to any incidents. Their training includes rope rescue skills, making them an integral part of the safety plan, reducing response times and minimising risk. This integrated safety approach gives asset managers peace of mind, knowing that a robust and effective rescue plan is always in place.
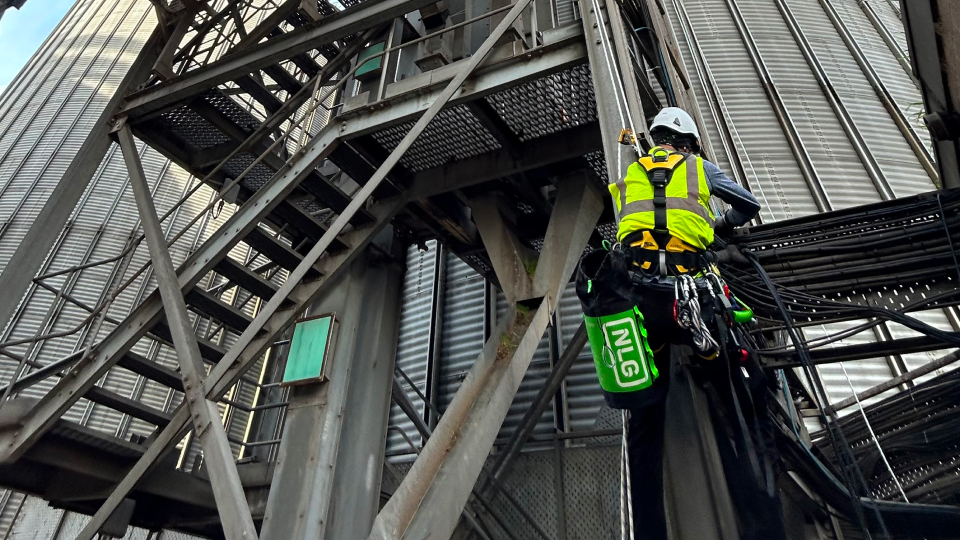
Environmental and cost benefits: Less is more
Another compelling argument for industrial rope access lies in its reduced environmental impact and cost-effectiveness. Scaffolding and powered platforms require significant materials and fuel for transport, setup, and operation. Rope access, being lightweight, demands fewer resources, which aligns well with the growing focus on sustainability in the industry.
Cost is another major consideration. By reducing setup time, labour requirements, and downtime, rope access offers significant savings. While the initial cost of hiring highly skilled rope access technicians may seem high, the overall savings in time, materials, and reduced operational disruption make it a more economical choice in the long run.
Versatility and adaptability: Tailored solutions for complex asset maintenance
Process industries present unique challenges when it comes to asset maintenance. Whether navigating tall structures like flare stacks or accessing intricate piping networks, each facility’s layout can pose obstacles to traditional access methods. Industrial rope access excels in such environments, providing tailored solutions that adapt to the specific needs of the task, no matter how complex or challenging.
This method is especially effective in environments where space is limited, and where scaffolding or powered platforms would be impractical or impossible. Whether performing non-destructive testing (NDT), cleaning, or painting large tanks and structures, rope access allows technicians to reach almost any part of a facility. Its versatility, combined with its minimal footprint, makes it the go-to solution for maintaining complex process industry assets.
Conclusion: A strategic move for process industry managers
For managers overseeing the integrity of assets in process industries, selecting the right access method for work at height is crucial. Industrial rope access not only meets but often exceeds the requirements for safety, efficiency, and cost-effectiveness. Its minimal footprint, rapid setup and removal, and adaptability to complex environments make it the ideal solution for industries where extended downtime is not an option, and every decision impacts the bottom line.
Rope access offers the strategic advantage needed to maintain productivity, ensure safety, and protect your assets. The next time you’re planning a project at height, consider whether rope access could be the key to unlocking better efficiency and value for your operation.
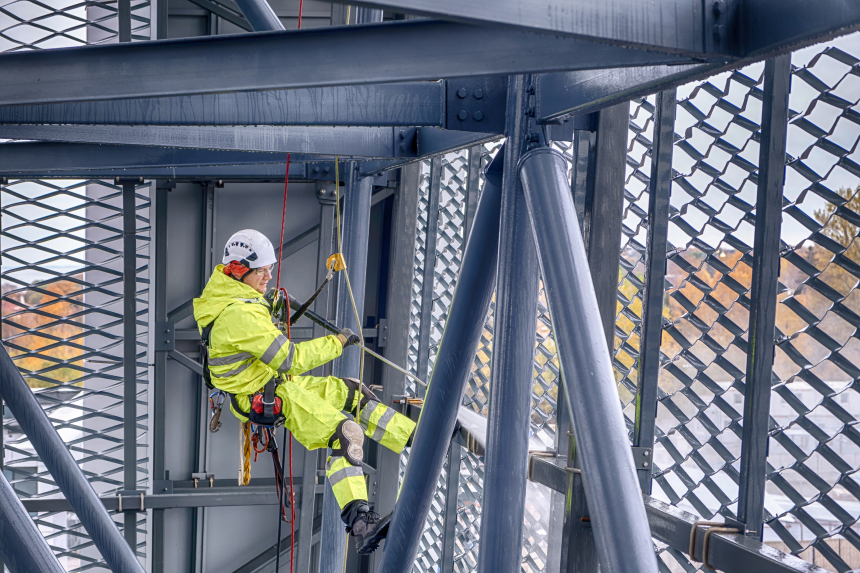